
Kalenji -TUNING
- yacool
- Zaprawiony W Bojach
- Posty: 13457
- Rejestracja: 03 gru 2008, 11:25
- Kontakt:
Ale masz super parapet! Wchodzisz do zespołu natychmiast. Będziesz odpowiedzialny za wizerunek firmy.
- wysek
- Zaprawiony W Bojach
- Posty: 3442
- Rejestracja: 16 paź 2004, 22:35
- Życiówka na 10k: 32:34
- Życiówka w maratonie: 2:43
- Lokalizacja: Lublin
- Kontakt:
-
- Wyga
- Posty: 78
- Rejestracja: 11 maja 2010, 10:48
- Życiówka na 10k: 00:40:50
- Życiówka w maratonie: 03:33:41
- Lokalizacja: Szmulki
Czuje się zaszczycony. Nie wiem tylko czy z tak poplątana przeszłością jak moja mogę odpowiadać za wizerunek, konkurencja może mi powyciągać pewne zaszłości.yacool pisze:Ale masz super parapet! Wchodzisz do zespołu natychmiast. Będziesz odpowiedzialny za wizerunek firmy.
Odpowiedzi szukaj w kodeksie Bushidō, lub po ciemnej stronie Mocy. Ewentualnie w sklepach z nożykami Victorinoxa.wysek pisze:Czym tak precyzyjnie ciachnąć podeszwę? Chce przerobić Kipruny 1000
Nie boję się gdy ciemno jest, bo mam latarkę i GPS
-
- Zaprawiony W Bojach
- Posty: 4947
- Rejestracja: 18 kwie 2009, 16:57
- Życiówka na 10k: brak
- Życiówka w maratonie: brak
I ja dojrzałem do tego by odchudzić parę Kalenji. Dzisiaj zaopatrzyłem się w nowe ostrza, jutro jadę po ofiary tego eksperymentu.
I tu pojawiły się pierwsze wątpliwości. Czytałem gdzieś, że aby wyciąć zapiętek trzeba kupić buty nieco mniejsze niż zazwyczaj. Jakie są Wasze odczucia w tym temacie? A może wycinanie zapiętka w Ekidenach nie ma sensu?
I tu pojawiły się pierwsze wątpliwości. Czytałem gdzieś, że aby wyciąć zapiętek trzeba kupić buty nieco mniejsze niż zazwyczaj. Jakie są Wasze odczucia w tym temacie? A może wycinanie zapiętka w Ekidenach nie ma sensu?
"Odbywający się przez skórę recykling energii poprawia obieg krwi, dostarczając więcej sił w życiu codziennym i sporcie." - Reebok
Buty "inspirowane są samochodowym systemem zawieszenia, który siłę uderzenia zamienia w napęd." - Adidas
Buty "inspirowane są samochodowym systemem zawieszenia, który siłę uderzenia zamienia w napęd." - Adidas
- yacool
- Zaprawiony W Bojach
- Posty: 13457
- Rejestracja: 03 gru 2008, 11:25
- Kontakt:
Odczuwam wywoływanie do tablicy.
Wycinanie zapiętka, a konkretnie usztywniającej tektury ma sens. Taki zabieg poprawia przyleganie buta do stopy w fazie największego odkształcenia podczas biegu. Im większa powierzchnia przylegania tym też lepsze czucie podłoża poprzez but. Nic nie sprężynuje, nic nie uwiera, nic nie odstaje. Wyprofilowana pod kształt łuku stopy podeszwa, poprawia trzymanie. But nie przemieszcza się na stopie i dobierając surowiec na przeróbkę można zredukować nieco początkowy luz podczas przymiarki. Niestety kalenji nie ma połówek w rozmiarówce, a szkoda. Jednak lekka konstrukcja i duża powierzchnia przylegania, skompensują ewentualny za duży luz i komfort zapewnimy po prostu mocniejszym sznurowaniem.
Jutro od rana Zenek ma do zrobienia kolejny tuning. Na stół trafi zamówienie od Jurka. Będę na żywo wrzucał foty po każdym cięciu.
Wycinanie zapiętka, a konkretnie usztywniającej tektury ma sens. Taki zabieg poprawia przyleganie buta do stopy w fazie największego odkształcenia podczas biegu. Im większa powierzchnia przylegania tym też lepsze czucie podłoża poprzez but. Nic nie sprężynuje, nic nie uwiera, nic nie odstaje. Wyprofilowana pod kształt łuku stopy podeszwa, poprawia trzymanie. But nie przemieszcza się na stopie i dobierając surowiec na przeróbkę można zredukować nieco początkowy luz podczas przymiarki. Niestety kalenji nie ma połówek w rozmiarówce, a szkoda. Jednak lekka konstrukcja i duża powierzchnia przylegania, skompensują ewentualny za duży luz i komfort zapewnimy po prostu mocniejszym sznurowaniem.
Jutro od rana Zenek ma do zrobienia kolejny tuning. Na stół trafi zamówienie od Jurka. Będę na żywo wrzucał foty po każdym cięciu.
- yacool
- Zaprawiony W Bojach
- Posty: 13457
- Rejestracja: 03 gru 2008, 11:25
- Kontakt:
Witam serdecznie ze słonecznej Addis Abeby. Komentować dla Państwa będzie Włodzimierz Szaranowisz i Dariusz Szpakowski. Jesteśmy na słynnym Meskel Square, gdzie tłumnie biegają mieszkańcy miasta. Mamy teraz godzinę 9:00 lokalnego czasu. O tej porze większość z tutejszych biegaczy jest już po drugim treningu i szykują się do wyjścia do pracy. Tym którzy pozostają w domu zaoferowaliśmy telemost Addis Abeba - Polska, w ramach dopołudniowego bloku edukacyjnego z cyklu: trawa czy grzyby.
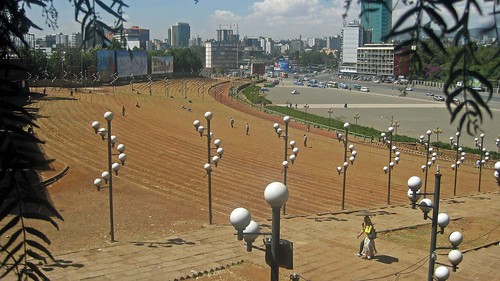
Podczas transmisji nauczać będziemy Etiopczyków naturalnego biegania oraz modyfikowania obuwia sportowego. Skupimy się zwłaszcza na tym drugim elemencie, ponieważ zaprosiliśmy do nas gościa specjalnego. Pan Zenon Marabut jest ekspertem od tuningowania butów i pokaże nam jak poprawnie zrobić samemu buty do naturalnego biegania.
Witamy Panie Zenku. Bardzo prosimy o przecięcie wstęgi i pozostawiamy Pana już sam na sam z czekającą na pomoc Afryką.

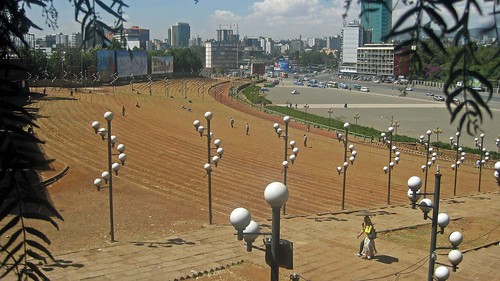
Podczas transmisji nauczać będziemy Etiopczyków naturalnego biegania oraz modyfikowania obuwia sportowego. Skupimy się zwłaszcza na tym drugim elemencie, ponieważ zaprosiliśmy do nas gościa specjalnego. Pan Zenon Marabut jest ekspertem od tuningowania butów i pokaże nam jak poprawnie zrobić samemu buty do naturalnego biegania.
Witamy Panie Zenku. Bardzo prosimy o przecięcie wstęgi i pozostawiamy Pana już sam na sam z czekającą na pomoc Afryką.

Ostatnio zmieniony 29 lis 2012, 13:23 przez yacool, łącznie zmieniany 1 raz.
- yacool
- Zaprawiony W Bojach
- Posty: 13457
- Rejestracja: 03 gru 2008, 11:25
- Kontakt:
Ponownie łączymy się z Panem Zenkiem.
Dzień dobry wszystkim telewidzom. Aby przygotować sobie wygodny but należy zastosować się do kilku wskazówek. Po pierwsze nie można się spieszyć, po drugie należy zawsze zaznaczać linie po których poprowadzony będzie nóż. Na zdjęciu poniżej pokazane są przyrządy do zaznaczania precyzyjnego cięcia (wszystkie opisane w dalszej części szczegóły i przybliżenia dotyczyć będą lewego buta).

Technika zaznaczania jest następująca: dociskamy mocno długopis do poziomu pianki z czarną gumą w tylnej części buta. But dociskamy do podłoża i pewnym ruchem okręcamy nim w jedną i drugą stronę, uzyskując linię boczną po obu stronach podeszwy. Taka technika pozwala na powtarzalność procesu.


Bardzo istotnym momentem jest wykończenie linii cięcia pod łukiem stopy. Ten element zaznaczony jest na poniższym zdjęciu. Proszę zwrócić uwagę na fabryczne przetłoczenia w piance. To one właśnie są wykorzystane jako punkty orientacyjne. Odwracamy bucik na plecki i ręcznie rysujemy łuki. Następnie płynnie łączymy je z wyznaczoną wcześniej linią.

Ten zabieg będzie miał kluczową rolę dla dalszego sterowania nożem.
Dzień dobry wszystkim telewidzom. Aby przygotować sobie wygodny but należy zastosować się do kilku wskazówek. Po pierwsze nie można się spieszyć, po drugie należy zawsze zaznaczać linie po których poprowadzony będzie nóż. Na zdjęciu poniżej pokazane są przyrządy do zaznaczania precyzyjnego cięcia (wszystkie opisane w dalszej części szczegóły i przybliżenia dotyczyć będą lewego buta).

Technika zaznaczania jest następująca: dociskamy mocno długopis do poziomu pianki z czarną gumą w tylnej części buta. But dociskamy do podłoża i pewnym ruchem okręcamy nim w jedną i drugą stronę, uzyskując linię boczną po obu stronach podeszwy. Taka technika pozwala na powtarzalność procesu.


Bardzo istotnym momentem jest wykończenie linii cięcia pod łukiem stopy. Ten element zaznaczony jest na poniższym zdjęciu. Proszę zwrócić uwagę na fabryczne przetłoczenia w piance. To one właśnie są wykorzystane jako punkty orientacyjne. Odwracamy bucik na plecki i ręcznie rysujemy łuki. Następnie płynnie łączymy je z wyznaczoną wcześniej linią.

Ten zabieg będzie miał kluczową rolę dla dalszego sterowania nożem.
- yacool
- Zaprawiony W Bojach
- Posty: 13457
- Rejestracja: 03 gru 2008, 11:25
- Kontakt:
Witamy ponownie po bardzo ciekawym bloku reklamowym telezakupów Mango. Przy okazji pozdrawiamy, zachwyconego nowym produktem, Zygmunta Hajzera.

Panie Zenku,
bardzo prosimy o ciąg dalszy.
Pierwsze cięcie rozpoczynamy zawsze od pięty.

Nóż prowadzimy precyzyjnie, zakosami po linii bocznej. Ostrze nie powinno pojawić się w środkowym wytłoczeniu podeszwy.

Dochodzimy do zaznaczonych łuków i zakosem szczytowym zaczynamy płynnie wychodzić z materiału.

Następnie zakosem nasadowym również podchodzimy pod czarną gumę.

Operację stosujemy naprzemiennie i płynnie kończymy cięcie.

Tym sposobem uzyskujemy kontrolowane wycięcie naddatku. Przy okazji odsłaniając jeden z systemów stosowanych obecnie w najnowszych butach sportowych. Tak zwany HHS czyli Hi Hole System, odciążający dolne partie mięśni nóg podczas biegu. Na zdjęciu widoczne są też ślady ukosowania po prowadzeniu noża.

Poniższe zdjęcie pokazuje skuteczną powtarzalność procesu, czego dowodem są podobnych kształtów, odpady produkcyjne.

Dalej widzimy zestawienie odpadów, na bazie których możemy ocenić cięcie. Odpad po prawej mówi nam, że cięcie zostało wykonane zbyt płytko.


Panie Zenku,
bardzo prosimy o ciąg dalszy.
Pierwsze cięcie rozpoczynamy zawsze od pięty.

Nóż prowadzimy precyzyjnie, zakosami po linii bocznej. Ostrze nie powinno pojawić się w środkowym wytłoczeniu podeszwy.

Dochodzimy do zaznaczonych łuków i zakosem szczytowym zaczynamy płynnie wychodzić z materiału.

Następnie zakosem nasadowym również podchodzimy pod czarną gumę.

Operację stosujemy naprzemiennie i płynnie kończymy cięcie.

Tym sposobem uzyskujemy kontrolowane wycięcie naddatku. Przy okazji odsłaniając jeden z systemów stosowanych obecnie w najnowszych butach sportowych. Tak zwany HHS czyli Hi Hole System, odciążający dolne partie mięśni nóg podczas biegu. Na zdjęciu widoczne są też ślady ukosowania po prowadzeniu noża.

Poniższe zdjęcie pokazuje skuteczną powtarzalność procesu, czego dowodem są podobnych kształtów, odpady produkcyjne.

Dalej widzimy zestawienie odpadów, na bazie których możemy ocenić cięcie. Odpad po prawej mówi nam, że cięcie zostało wykonane zbyt płytko.

Ostatnio zmieniony 29 wrz 2011, 20:32 przez yacool, łącznie zmieniany 3 razy.
-
- Zaprawiony W Bojach
- Posty: 1374
- Rejestracja: 08 maja 2009, 08:32
Halo, halo Włodku ... halo, halo Darku. Moje pytanie do mistrza Zenona jest banalne ale w tym momencie dla Mnie kluczowe. Czym nasmarować stopy żeby nie swędziały? Nie mogą się doczekać chwili nim dotkną tych perełek.
To mówiłem Ja ...
To mówiłem Ja ...
- yacool
- Zaprawiony W Bojach
- Posty: 13457
- Rejestracja: 03 gru 2008, 11:25
- Kontakt:
Mamy jakieś kłopoty na łączu. Za chwilkę wejdziemy na antenę ponownie. Tymczasem zapraszamy do reklamy.
-
- Wyga
- Posty: 68
- Rejestracja: 26 lip 2009, 02:35
Korzystając z przerwy w transmisji chciałem się dopytać ktoregoś z widzów siedzących obok mnie: "Jak złożyć zamówienie na ten towar"? A może Maestro zza srebrnego ekranu odpowie? Yacool, robisz te buty tylko dla wybrańców? Ile by kosztowało skrojenie parki dla mnie?
Przyciałem ostatnio swoje stratusy (podeślę zdjęcia na forum w wolnej chwili) ale duzo im brakuje do dzieł Mistrza. Obiecuję, że te od Ciebie będę bardzo szanował i biegał w nich tylko w niedzielę do kościoła.
Przyciałem ostatnio swoje stratusy (podeślę zdjęcia na forum w wolnej chwili) ale duzo im brakuje do dzieł Mistrza. Obiecuję, że te od Ciebie będę bardzo szanował i biegał w nich tylko w niedzielę do kościoła.
- yacool
- Zaprawiony W Bojach
- Posty: 13457
- Rejestracja: 03 gru 2008, 11:25
- Kontakt:
Jesteśmy ponownie.
Kontrola, kontrola i jeszcze raz kontrola. To klucz do sukcesu. Nie podpalajmy się za bardzo, bo zniszczymy but zanim się urodzi.
Poniżej proces kontrolny pomiaru grubości odpadu. Grubość może wahać się w granicach 14 do 17 milimetrów. Pozostawiając sobie większy zapas (mniejsza grubość odpadu), wydłużamy czas szlifowania ale też mamy szansę na lepszy efekt końcowy.

Następnie nacinamy podeszwę pod wstępne ukształtowanie czubka buta. Ostrożnie wcinamy się w czarną gumę i często sprawdzamy czy pojawiła się już biała szczelina. Prawy zakos prowadzimy po fabrycznym przetłoczeniu. Lewy zakos pozostawiam pod indywidualne preferencje tuner-domatora. Poziome cięcie łączy oba zakosy.


Po wstępnych nacięciach zrywamy podeszwę i odsłaniamy piękno, kryjące się dotąd przed naszymi oczami. Tutaj uwaga praktyczna: tak ładnie odrywana, całymi płatami, guma jak widać na zdjęciach poniżej, świadczy o tym, że but jest świeżo wyprodukowany i nie leżał długo na półce. Gdy guma się rwie to szlag mnie trafia, bo proces wydłuża się o parę godzin. No ale wiadomo jak to jest ze starym mięsem.


Jak łatwo się przekonać proces oprawiania nie wymaga wirtuozerii i chętnie zleciłbym go swoim uczniom.

Zdjęcie poglądowe

...i szczegół po oprawieniu

- Dobra, czas na fajkę. @#$%^ jak mnie łapa napier...
- Przepraszamy mamy kłopot z fonią. Panie Zenku jest Pan wciąż na antenie.
- A tak... przepraszam.
- Mamy sygnał od telewidza odnośnie złożenia zamówienia na Pana produkty.
- Buciki można zamawiać poprzez pw mojej kliniki.
Bardzo dziękujemy i zapraszamy ponownie za chwilę.
Kontrola, kontrola i jeszcze raz kontrola. To klucz do sukcesu. Nie podpalajmy się za bardzo, bo zniszczymy but zanim się urodzi.
Poniżej proces kontrolny pomiaru grubości odpadu. Grubość może wahać się w granicach 14 do 17 milimetrów. Pozostawiając sobie większy zapas (mniejsza grubość odpadu), wydłużamy czas szlifowania ale też mamy szansę na lepszy efekt końcowy.

Następnie nacinamy podeszwę pod wstępne ukształtowanie czubka buta. Ostrożnie wcinamy się w czarną gumę i często sprawdzamy czy pojawiła się już biała szczelina. Prawy zakos prowadzimy po fabrycznym przetłoczeniu. Lewy zakos pozostawiam pod indywidualne preferencje tuner-domatora. Poziome cięcie łączy oba zakosy.


Po wstępnych nacięciach zrywamy podeszwę i odsłaniamy piękno, kryjące się dotąd przed naszymi oczami. Tutaj uwaga praktyczna: tak ładnie odrywana, całymi płatami, guma jak widać na zdjęciach poniżej, świadczy o tym, że but jest świeżo wyprodukowany i nie leżał długo na półce. Gdy guma się rwie to szlag mnie trafia, bo proces wydłuża się o parę godzin. No ale wiadomo jak to jest ze starym mięsem.


Jak łatwo się przekonać proces oprawiania nie wymaga wirtuozerii i chętnie zleciłbym go swoim uczniom.

Zdjęcie poglądowe

...i szczegół po oprawieniu

- Dobra, czas na fajkę. @#$%^ jak mnie łapa napier...
- Przepraszamy mamy kłopot z fonią. Panie Zenku jest Pan wciąż na antenie.
- A tak... przepraszam.
- Mamy sygnał od telewidza odnośnie złożenia zamówienia na Pana produkty.
- Buciki można zamawiać poprzez pw mojej kliniki.
Bardzo dziękujemy i zapraszamy ponownie za chwilę.
- Ernisimo
- Wyga
- Posty: 76
- Rejestracja: 23 mar 2010, 10:56
tirli pisze:Korzystając z przerwy w transmisji chciałem się dopytać ktoregoś z widzów siedzących obok mnie: "Jak złożyć zamówienie na ten towar"? A może Maestro zza srebrnego ekranu odpowie? Yacool, robisz te buty tylko dla wybrańców? Ile by kosztowało skrojenie parki dla mnie?
Przyciałem ostatnio swoje stratusy (podeślę zdjęcia na forum w wolnej chwili) ale duzo im brakuje do dzieł Mistrza. Obiecuję, że te od Ciebie będę bardzo szanował i biegał w nich tylko w niedzielę do kościoła.
Polecam konkursy jako wstępne eliminację dla chętnych użytkowników. Sam stałem się posiadaczem arcydzieła "Kalenji ZEN" w ten własnie sposób
Należy jednak pamiętać o fizycznym zmęczeniu dłoni Doktora (wartość unikalna) oraz psychicznym wyczerpaniu portfela Doktora (wartość policzalna) więc ..... czekamy na konkurs (ja oczywiście jestem już poza konkursem

